Gigacasting has swiftly taken the automotive industry by storm. As technology evolves, gigacasting emerges as a solution to many of the challenges faced by automakers. Let’s dive into this trend and understand its significance.
What is Gigacasting?
Gigacasting is a cutting-edge manufacturing process that allows automakers to create large, integrated parts from molten metal in a single mould. This eliminates the need for joining smaller parts together, resulting in a more solid and durable component.
Key Advantages:
- Reduced Assembly Time: Fewer components mean less time spent on assembly.
- Enhanced Strength: Single-cast parts are inherently stronger, reducing weak points.
- Weight Reduction: Reducing the number of joins and fasteners can lead to a lighter overall component.
- Cost Efficiency: With fewer parts to produce and assemble, production costs can be lowered.
Gigacasting vs. Traditional Manufacturing
Traditional car manufacturing involves creating many individual parts and subsequently joining them together. Gigacasting challenges this approach by enabling the creation of larger, more integrated parts.
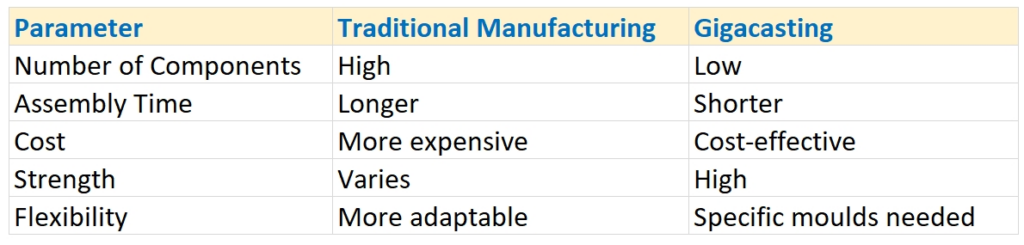
As we transition to an era of electric vehicles (EVs) and sustainability, gigacasting’s role becomes ever more crucial. With EVs requiring fewer parts than their internal combustion counterparts, the potential for gigacasting to streamline production is immense.
Parts benefiting from Gigacasting:
- Battery Enclosures for EVs: Gigacasting can produce strong, protective casings for batteries.
- Chassis Components: Integrated, single-piece chassis parts can enhance vehicle strength and durability (front, rear, underbody)
- Interior Structures: Simplifying the intricate components inside a car can lead to better design and increased space.
Despite its benefits, gigacasting isn’t without its challenges. Manufacturing large parts requires large moulds and machines, demanding significant investments. Additionally, errors in a gigacast part can be costlier due to the part’s size and integration.
But it seems that Gigacasting is undeniably shaping the future of car manufacturing. With its potential to revolutionise production processes, reduce costs, and enhance vehicle quality, it’s clear to see why more and more vehicle manufacturer are going to use those processes:
Ford, (testing IDRA Gigapress), GM, Hyundai (Hypercasting), Lexus, Mercedes, NIO, Tesla (Pioneer, 14 Gigapresses from IDRA), Toyota, Volvo (Two Gigapresses from Bühler), Volkswagen, Xpeng and Zeekr are already using or going to use this technology.
As above and other OEMs continue to innovate and seek efficiencies, gigacasting will undoubtedly play a pivotal role in the future evolution of car manufacturing.
Read our Market Research Document related to Gigacasting here [PDF]